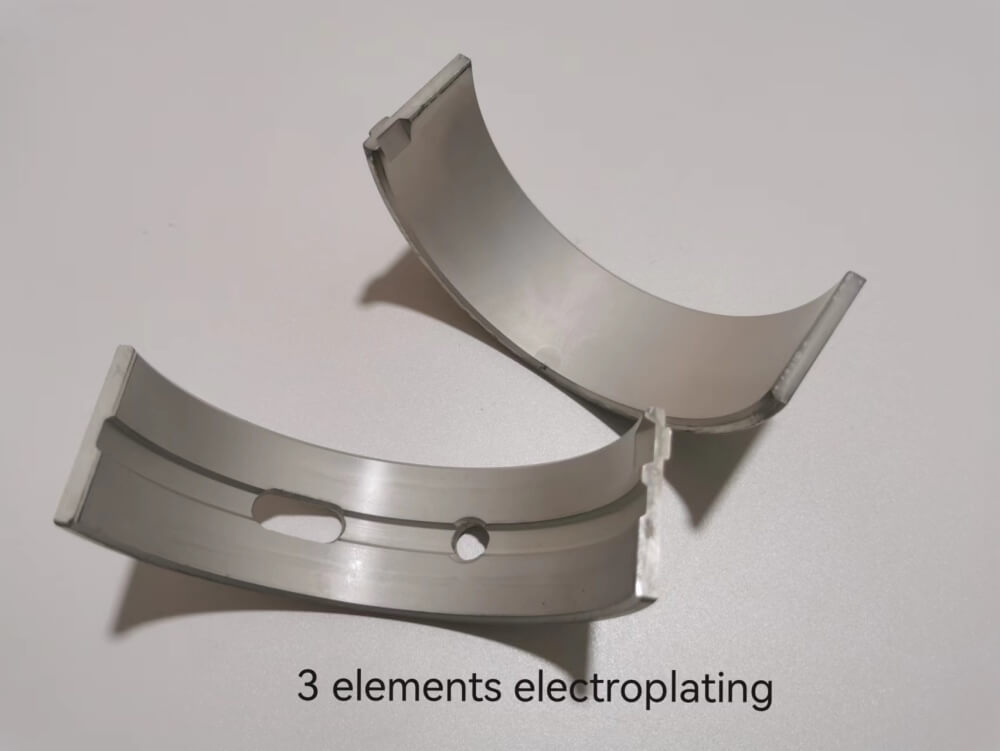
First is the most common kind we use, electroplating bearing. Left picture is main kind – 3 elecments electroplating bearing.
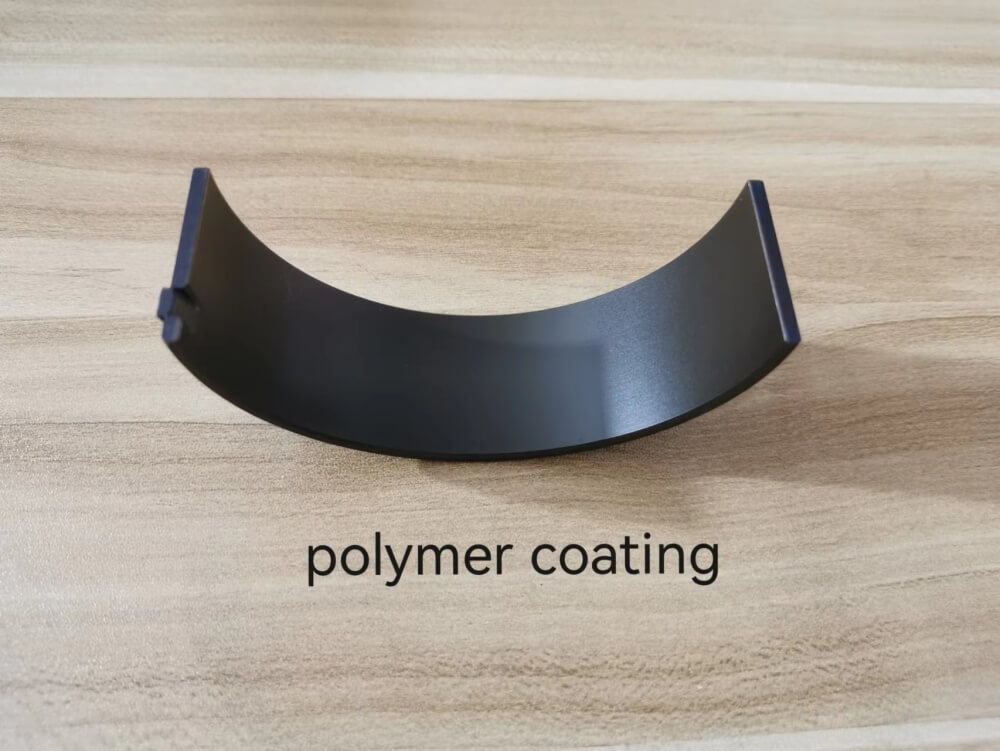
Second is the updated technolog – polymer coating bearing.
For aftermarket market, this technology just start, but will be a main new choice in future.
Why to say like this? Let us see coating process.
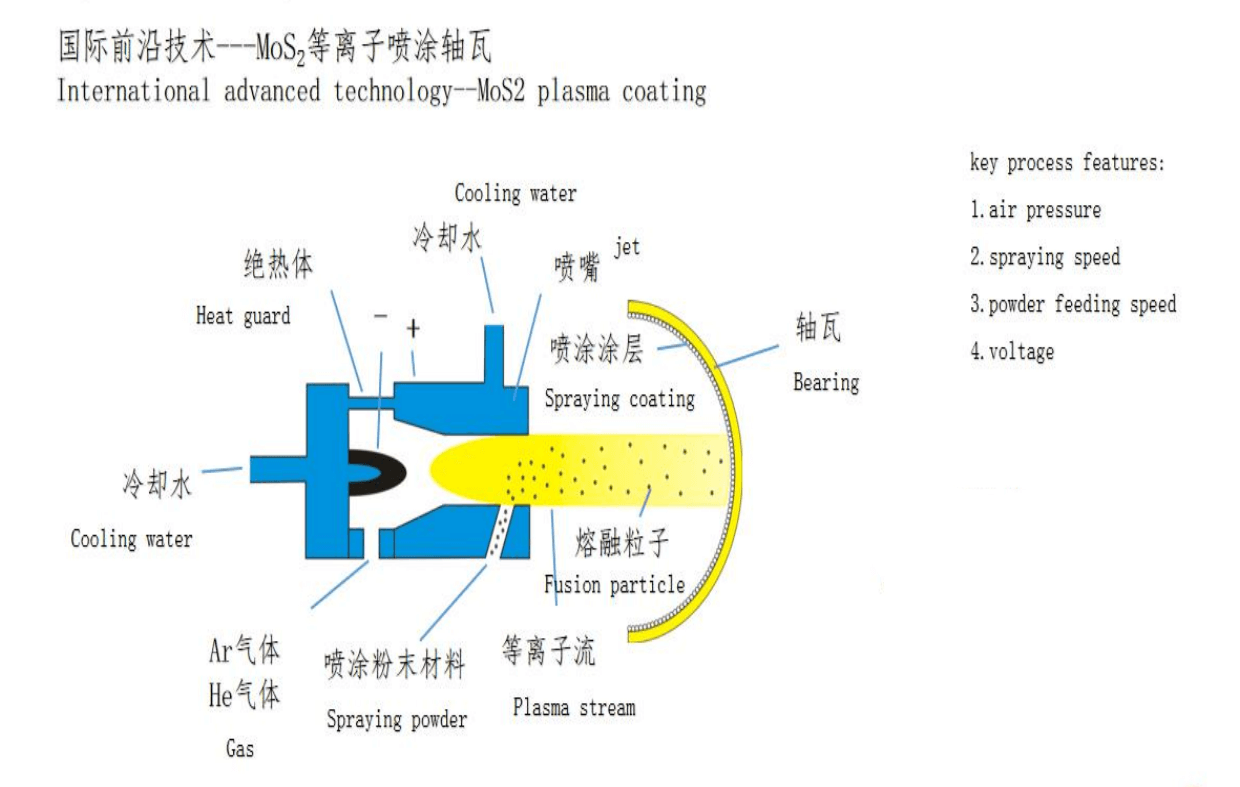
From the process, you can find that the process is higher efficiency than electroplating. Then is lower emissions. This is more friendly to our environment, so lower pollutant treatment costs for factory.
But you may say that we need better function, not lower factory cost, repair engine cost is very high, for truck and exvacator stop mean money go away.
Of course, it is better than traditional 3 elements electroplating. It is decided by material. Coating powder is self-lubricating material like molybdenum disulfide, graphite, it can help decrease friction coefficient, also these material can bear very wide range temperature, from -200~300°C, it is suitable for engine different working process like start stop in different weather. Also these material can work in high load high speed environement, no need lubricating oil.
What better function u can get from polymer bearing?
• Excellent anti friction and wear resistance properties.
• The polymer coating improves the bearing’s compatibility.
• High load capacity bearings with outstanding seizure resistance.
• Especially suitable for start-stop and hybrid engines that operate constantly under metal-to-metal contact.
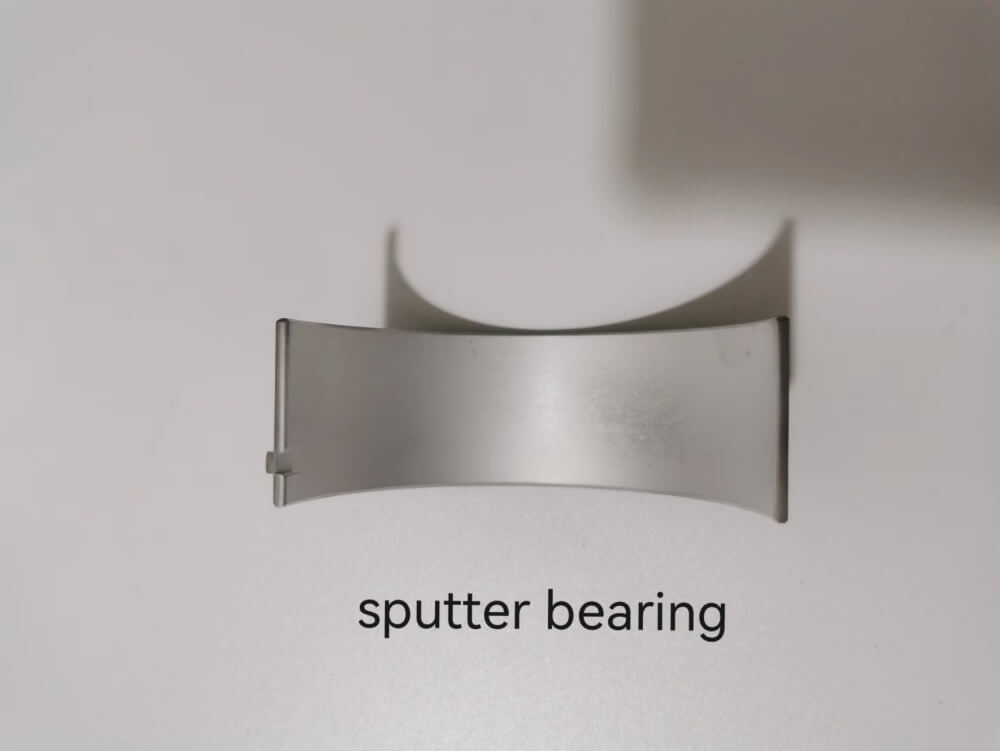
Yes, left picture is sputter bearing, but many people may take it as 3 elements electroplating bearing. For few in market, only professional people can tell, or a closer look reveals the difference in appearance.
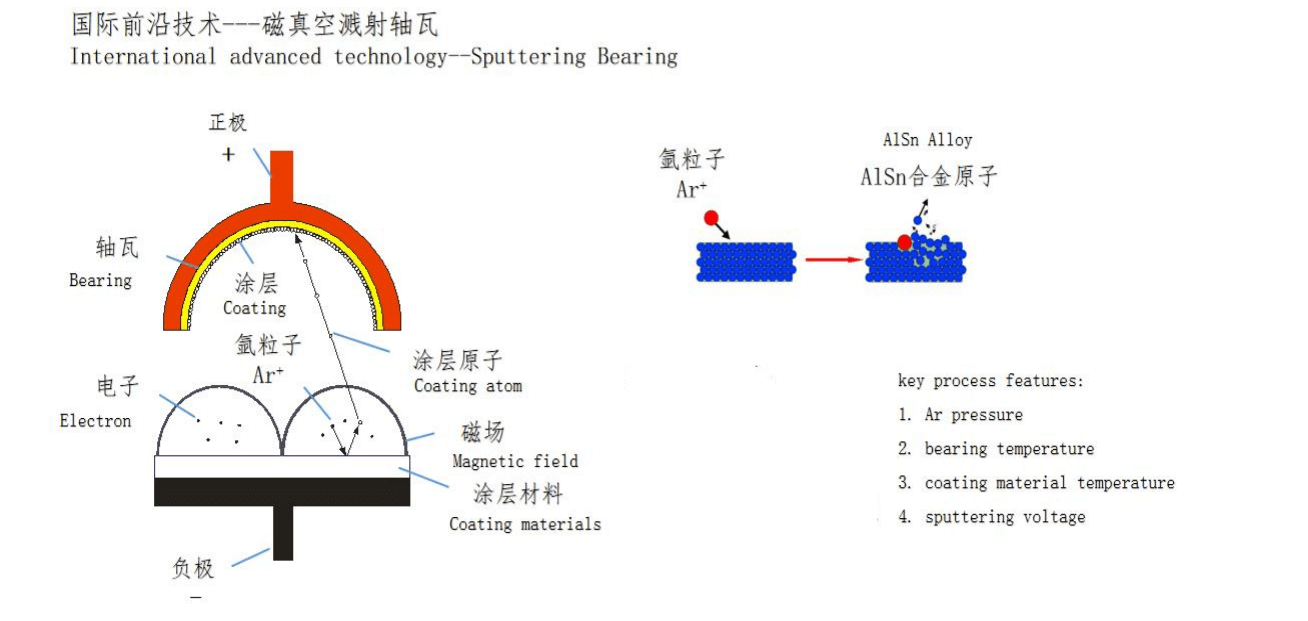
Left picture is sputter bearing process. We call it PVD (Physical Vapour Deposition) process. This sliding layer is considerably thinner and more resistant to wear than on conventional bearing shells. Sputter bearing is mainly designed for turbocharged diesel engine.
For this technolog production cost is very high, for both expensive production equipment and very long production time, it is very diffcult to reach the industrial level requirements.
So here just a simple introduction.